Introduction
Workplace safety is a paramount concern across all industries in Canada. Maintaining safe and healthy working environments is not only a legal obligation for employers but also a moral responsibility. A significant part of ensuring workplace safety is adhering to Canadian safety regulations.
In this blog post, we will delve into the essential standard procedures that govern workplace safety in Canada, offering insights into the key Canadian workplace safety regulations and how they are implemented. We will also explore the importance of these procedures and their adaptability to industry-specific standards.
In this blog post, we will delve into the essential standard procedures that govern workplace safety in Canada, offering insights into the key Canadian workplace safety regulations and how they are implemented. We will also explore the importance of these procedures and their adaptability to industry-specific standards.
Key Canadian Workplace Safety Regulations
In Canada, workplace safety is governed by a comprehensive set of regulations and standards designed to ensure the well-being of employees and prevent accidents and injuries on the job. The key regulatory framework that guides workplace safety in Canada includes the Occupational Health and Safety Act, often referred to as OHSA, and its corresponding regulations. OHSA mandates employers to provide a safe working environment, which includes properly maintaining equipment and machinery, implementing safe work procedures, and ensuring employees have access to necessary protective gear.
Another fundamental piece of legislation is the Canada Labour Code, which applies to federal workplaces and sets the standards for health and safety for federal employees. Under this code, employers must assess and mitigate risks, establish hazard prevention programs, and educate employees about safety measures. It also outlines employees' rights to refuse unsafe work.
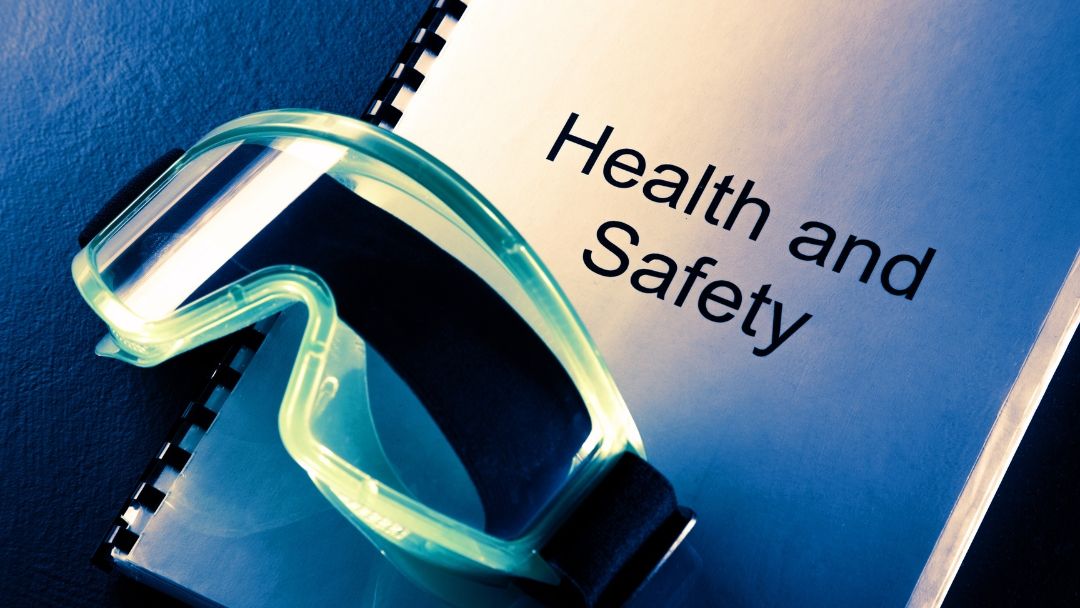
On a provincial level, each Canadian province has its own set of workplace safety regulations. These provincial regulations often align with federal standards while also addressing unique regional concerns. It's important for both employers and employees to familiarize themselves with the specific regulations that apply to their province.
Prominent among these provincial regulations is the Workers' Compensation Act, which mandates workplace safety and provides compensation for employees who sustain work-related injuries or illnesses.
Additionally, the Workplace Hazardous Materials Information System (WHMIS) is a significant regulation that governs the labeling and handling of hazardous materials in workplaces across Canada. WHMIS ensures that employees are aware of the potential dangers posed by the materials they work with and provides guidelines for the safe use, storage, and disposal of these substances.
These Canadian workplace safety regulations, along with numerous others, play a pivotal role in fostering a safe and secure work environment, protecting employees' well-being, and minimizing accidents and incidents on the job. Employers must stay vigilant in adhering to these regulations, fostering a culture of safety, and continuously educating their workforce to maintain a healthy and productive work atmosphere.
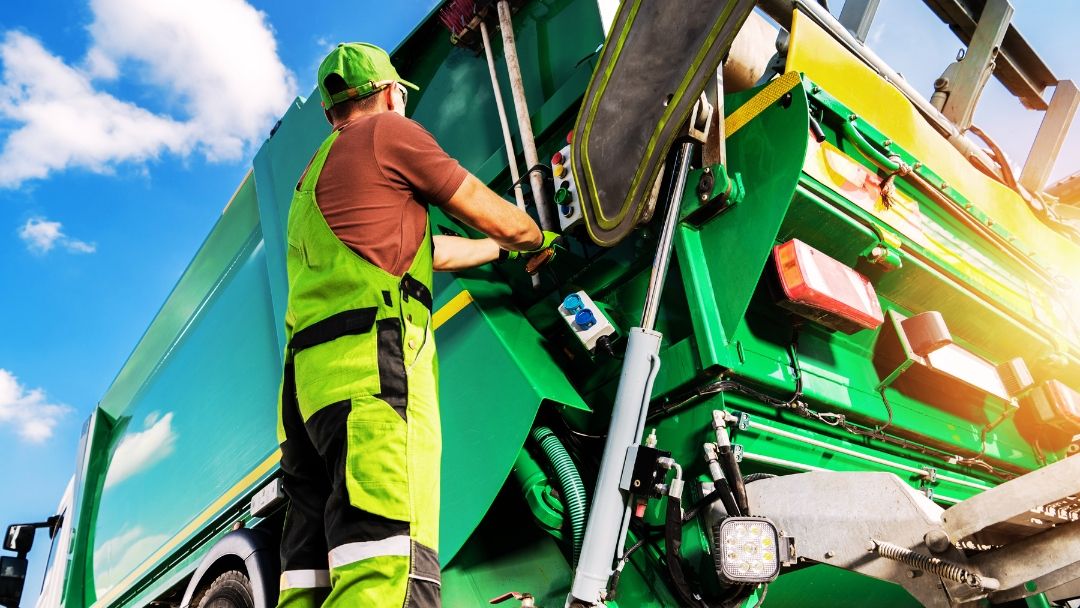
Establishing Standard Safety Procedures
One of the cornerstones of workplace safety in Canada is the establishment of standard safety procedures. These procedures are critical in maintaining a work environment that is free from accidents and injuries. They provide a framework for addressing various safety concerns and ensuring the well-being of all employees.
To begin, it's crucial for organizations to identify and assess potential hazards in their workplaces. This risk assessment forms the foundation for developing safety procedures tailored to the specific risks present in each workplace. Identifying hazards can include inspecting equipment, assessing work processes, and considering the use of hazardous materials.
Once potential hazards have been identified, organizations must develop safety procedures designed to mitigate these risks. These procedures should be comprehensive and cover a range of safety aspects, such as emergency response protocols, fire safety measures, equipment usage guidelines, and personal protective equipment (PPE) requirements. Employers are responsible for regularly reviewing and updating these procedures to ensure they remain effective and relevant.
To begin, it's crucial for organizations to identify and assess potential hazards in their workplaces. This risk assessment forms the foundation for developing safety procedures tailored to the specific risks present in each workplace. Identifying hazards can include inspecting equipment, assessing work processes, and considering the use of hazardous materials.
Once potential hazards have been identified, organizations must develop safety procedures designed to mitigate these risks. These procedures should be comprehensive and cover a range of safety aspects, such as emergency response protocols, fire safety measures, equipment usage guidelines, and personal protective equipment (PPE) requirements. Employers are responsible for regularly reviewing and updating these procedures to ensure they remain effective and relevant.
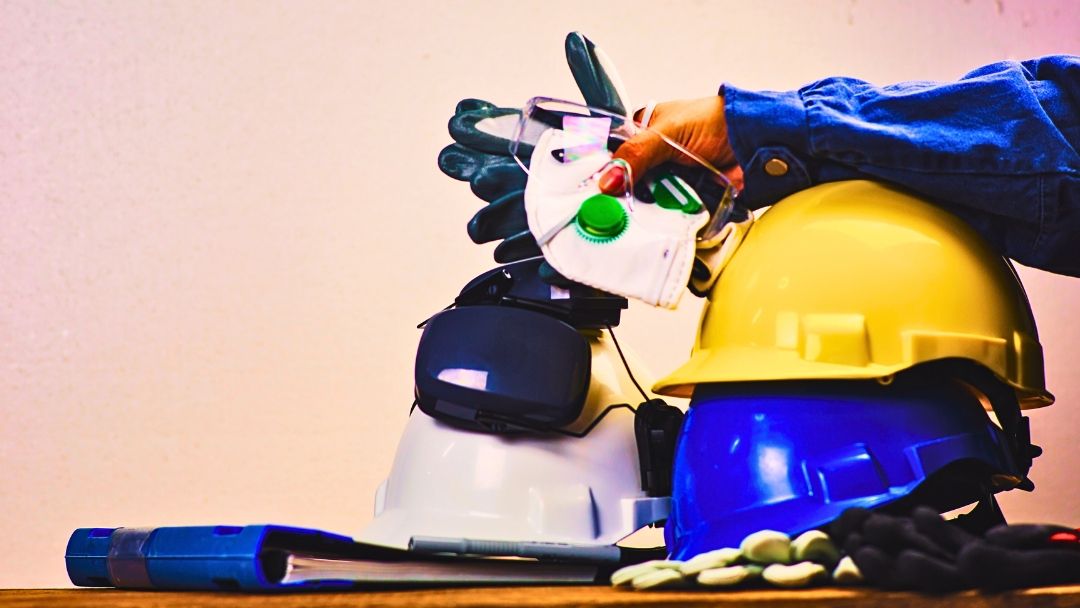
Another important component of standard safety procedures is safety training for all employees. This training should include information about potential hazards, the safe operation of equipment, and how to respond to emergencies. It is essential to keep detailed records of all safety training and ensure that employees are aware of the safety procedures in place.
To enforce and maintain these safety procedures, organizations should appoint safety officers or committees responsible for monitoring safety practices, conducting safety audits, and addressing any safety concerns that arise. This includes investigating accidents or near misses and implementing corrective actions to prevent recurrence.
Standard safety procedures also encompass preventive measures like regular equipment maintenance, housekeeping, and promoting a culture of safety within the workplace. Employees should feel encouraged to report safety concerns or incidents without fear of retaliation.
By adhering to and continuously improving standard safety procedures, Canadian workplaces can create environments where employees feel protected, valued, and confident in their safety. These procedures are integral to safeguarding the health and well-being of the workforce and reducing the risk of accidents and injuries.
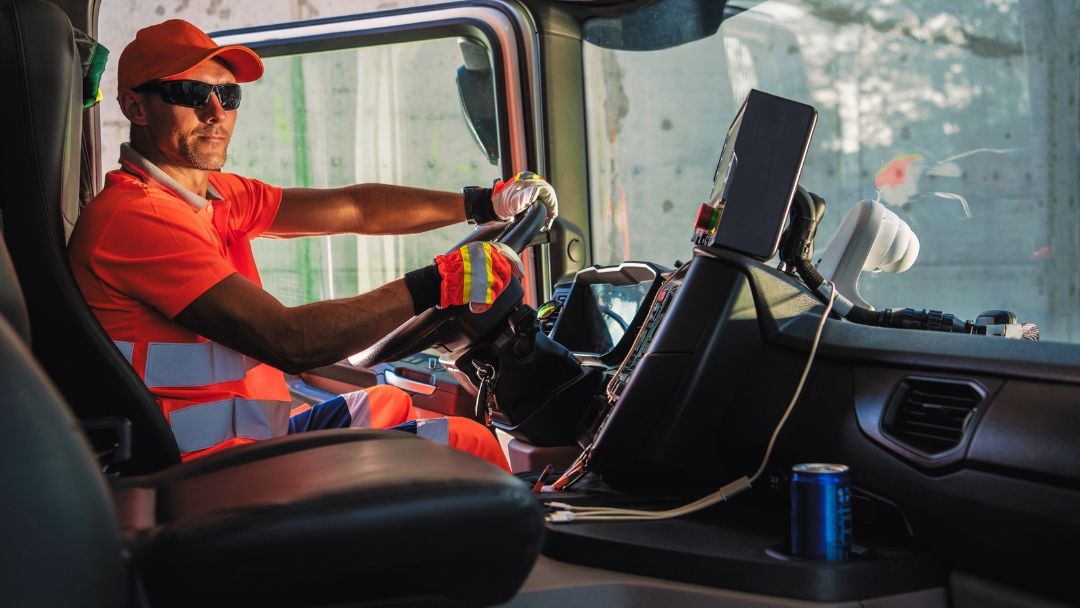
Implementing Safety Protocols
In Canada, workplace safety is a top priority, and one of the key elements in achieving this is the implementation of safety protocols. These protocols provide a structured framework for organizations to follow, ensuring that safety measures are effectively integrated into their day-to-day operations.
First and foremost, implementing safety protocols involves clear and transparent communication. This means that safety guidelines, procedures, and expectations must be communicated to all employees, contractors, and anyone who enters the workplace. This information should be easy to access and understand, fostering a culture of safety awareness.
Safety protocols often include preventive measures aimed at reducing the risk of accidents and injuries. Regular equipment maintenance is one such preventive measure. By adhering to strict maintenance schedules and safety checks, organizations can minimize the likelihood of equipment failures that could result in accidents. This includes regular inspections, repairs, and replacement of faulty equipment.
Emergency response protocols are also a crucial aspect of safety implementation. In the event of accidents, fires, or any other emergency situation, having clear protocols in place can mean the difference between a contained incident and a catastrophic one. These protocols should specify how employees should respond, what emergency equipment is available, and where designated assembly points are located.
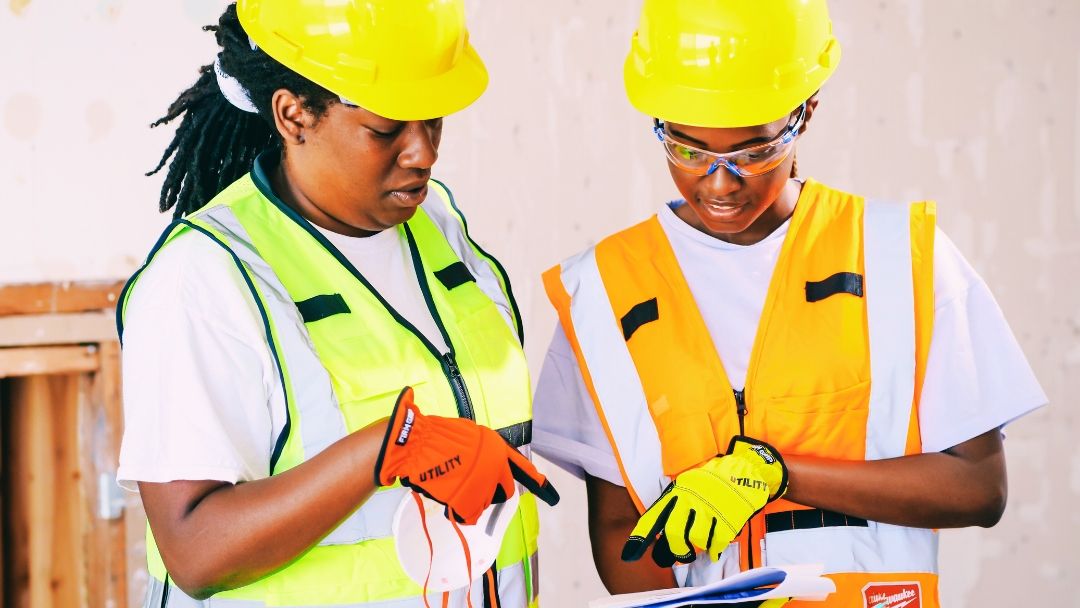
Furthermore, safety protocols encompass the use of personal protective equipment (PPE). It is essential to ensure that employees have easy access to the necessary PPE required for their tasks, whether it's helmets, gloves, safety glasses, or specialized gear. Organizations must also enforce the use of PPE when and where it is deemed necessary.
Consistent and ongoing training is another key element of implementing safety protocols. Employees should receive regular safety training to ensure they are aware of potential risks and how to mitigate them. This training could cover areas such as emergency evacuation procedures, handling hazardous materials, and the proper use of safety equipment.
In addition to communication, preventive measures, emergency response, and training, organizations must establish mechanisms for monitoring and enforcing safety protocols. Safety officers or committees may conduct regular inspections, audits, and assessments to ensure compliance. Furthermore, safety protocols should be periodically reviewed and updated to reflect any changes in regulations, technology, or work processes.
By implementing safety protocols consistently and comprehensively, organizations in Canada can foster a safe and secure work environment where employees can thrive without compromising their well-being. It is a vital part of the commitment to keeping the workforce and workplaces safe and protected from potential hazards.
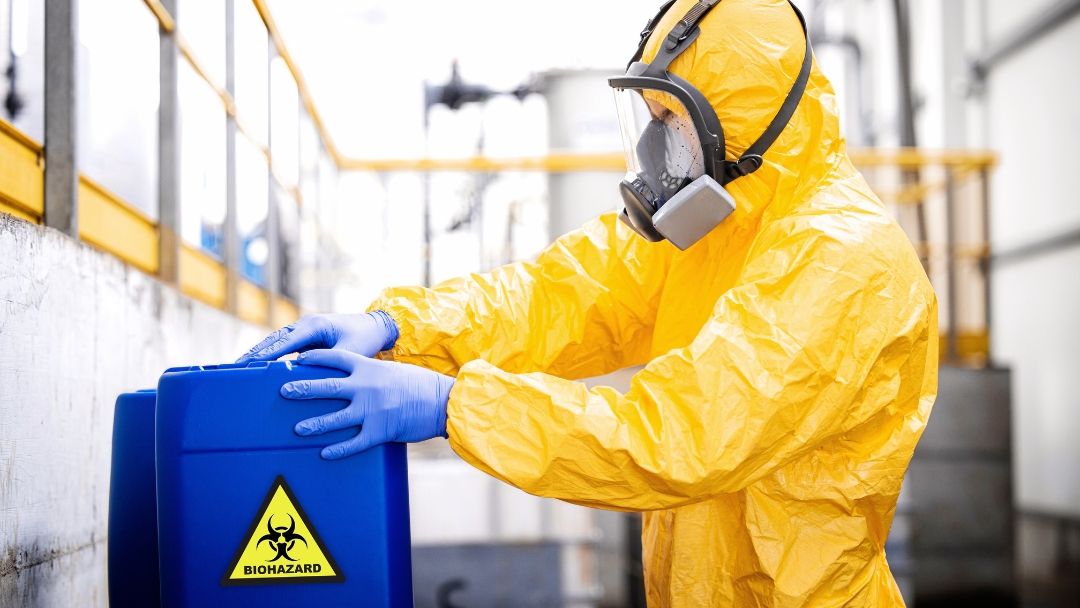
Safety Inspections and Reporting
In the realm of workplace safety in Canada, safety inspections and reporting are indispensable components. These processes are essential for identifying potential hazards, ensuring compliance with regulations, and maintaining a safe working environment.
Safety inspections involve regular assessments of the workplace, its equipment, and its processes. These inspections are typically carried out by safety officers or dedicated safety committees within an organization. The primary objective is to identify hazards or unsafe conditions before they lead to accidents. This process also assesses whether safety protocols are being followed as prescribed.
During these inspections, potential hazards are documented, and their severity is evaluated. Hazard reports can range from minor issues like a loose handrail to more critical concerns such as malfunctioning machinery or the lack of proper ventilation in workspaces. Each report should detail the nature of the hazard, its location, the potential risks, and any recommended corrective actions.
Once a hazard is identified, it is essential to promptly address and mitigate it. If immediate action is required to ensure the safety of employees, work should cease in the affected area until the hazard is resolved. In the case of minor issues, corrective actions can be planned, scheduled, and carried out within a reasonable timeframe.

To ensure transparency and accountability, safety reports and inspections are subject to meticulous record-keeping. These records are not only used to track issues and resolutions but also to monitor trends and areas where recurrent problems arise. This historical data can inform the organization's safety strategy and help in preventing future accidents.
Furthermore, safety reporting encompasses a crucial aspect of a culture of transparency and accountability in the workplace. It allows employees to report unsafe conditions, incidents, or near-misses without fear of repercussions. Reporting can be done through various channels, such as incident reports, safety suggestion boxes, or confidential meetings with designated safety personnel.
When an incident does occur, it is equally important to investigate and report on the event thoroughly. This includes documenting what happened, why it happened, and what measures need to be implemented to prevent a recurrence. Incident reports provide valuable insights for learning from mistakes and continually improving safety measures.
By incorporating safety inspections and reporting into standard procedures, Canadian organizations ensure that potential hazards are identified and rectified promptly. This commitment to regular evaluation and reporting is a fundamental element in fostering a culture of safety in workplaces across the country.
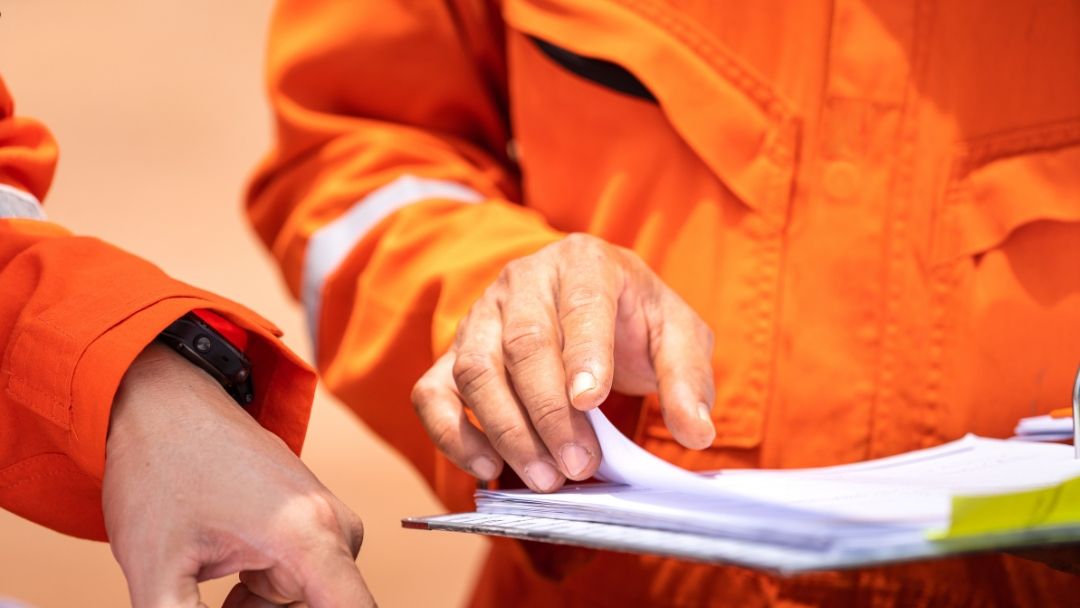
Adapting to Industry-Specific Standards
Workplace safety standards in Canada are not one-size-fits-all. They often vary based on the industry, the nature of the work, and the specific risks involved. As such, adapting to industry-specific standards is a fundamental aspect of maintaining safety in Canadian workplaces.
Each industry has its own unique set of risks and safety challenges. For example, construction sites face hazards related to heavy machinery, heights, and potentially hazardous materials. In contrast, an office environment may have different concerns, such as ergonomics and fire safety. To address these differences, federal and provincial regulations often provide industry-specific guidelines and standards that employers must follow.
Adapting to these industry-specific standards means that employers and employees must stay well-informed about the requirements relevant to their particular field. It involves a combination of regulations set at different levels of government, industry-specific associations, and best practices recognized in the field.
Each industry has its own unique set of risks and safety challenges. For example, construction sites face hazards related to heavy machinery, heights, and potentially hazardous materials. In contrast, an office environment may have different concerns, such as ergonomics and fire safety. To address these differences, federal and provincial regulations often provide industry-specific guidelines and standards that employers must follow.
Adapting to these industry-specific standards means that employers and employees must stay well-informed about the requirements relevant to their particular field. It involves a combination of regulations set at different levels of government, industry-specific associations, and best practices recognized in the field.
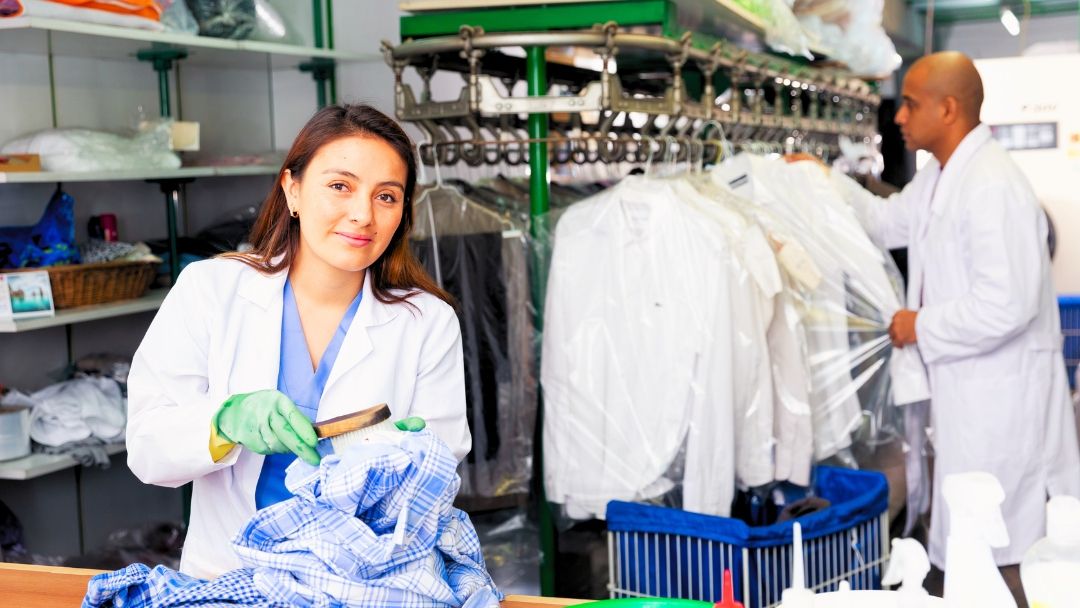
One significant aspect of adapting to industry-specific standards is education and training. Employers are responsible for ensuring that their employees are well-versed in industry-specific safety protocols. This often includes specialized training programs, certifications, and ongoing education. For example, a worker on an oil rig will require different training compared to someone working in a laboratory.
In some industries, these standards may be established and monitored by regulatory bodies. For example, the nuclear energy sector has its unique regulatory framework governed by the Canadian Nuclear Safety Commission (CNSC). The mining industry adheres to regulations administered by Natural Resources Canada, and the transportation sector follows guidelines provided by Transport Canada.
Adapting to industry-specific standards is not only about complying with regulations but also about embracing a culture of safety that aligns with the specific risks of the job. This involves consistently updating safety measures, incorporating new technology, and fostering a work environment where safety is paramount.
Ultimately, adapting to industry-specific standards in Canada is crucial for the safety and well-being of employees. It is about understanding the unique risks and challenges within each sector and proactively addressing them to prevent accidents and injuries. By doing so, organizations ensure that their workforce remains safe and that they remain compliant with the law.
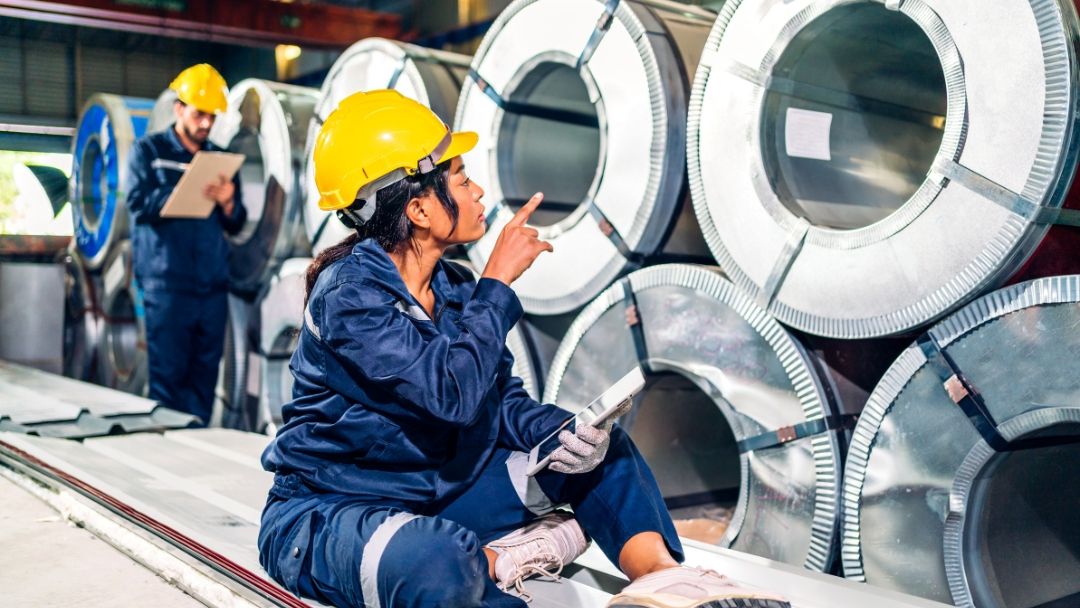
Conclusion
In Canada, workplace safety is more than a legal requirement; it's a shared commitment to preserving the well-being of employees across diverse industries. The key Canadian workplace safety regulations, from the Canadian Occupational Health and Safety (OHS) requirements to industry-specific standards, provide a robust framework for employers to build safe workplaces.
Implementing standard safety procedures, establishing safety protocols, conducting regular safety inspections, and adapting to industry-specific standards are the cornerstones of an effective safety program. Through this, employers demonstrate their dedication to creating and maintaining safe work environments that safeguard employees and, in turn, their organizations.
As we conclude this exploration of workplace safety in Canada, it's clear that adhering to standard procedures is just the beginning. Employers, employees, and regulators alike must work in unison to foster a culture of safety that transcends the law, becoming a shared value in Canadian workplaces. By doing so, we ensure not only legal compliance but the health, well-being, and longevity of our workforce. Workplace safety is not just a regulation; it's a promise that Canadian employers are steadfastly keeping.
Level up your workplace safety!